|
|
 |
Arched roof storage tank mechanical cleaning |
Time:2023/12/7 View:2047 |
During the use of the oil storage tank, impurities in the crude oil will be deposited on the bottom and wall of the tank, reducing the effective volume of the oil storage tank, so regular maintenance and removal of sludge are required. According to the provisions of relevant industry standards, the maintenance cycle of oil storage tanks is usually 5 to 7 years, and the storage tanks must be cleaned before the maintenance. The cleaning method of storage tanks can be divided into manual cleaning and mechanical cleaning. According to the mechanical cleaning principle of large crude oil storage tank, BJATL cleans the floating top tank through process modification. First, the floating top column is extracted according to the number and position required by the process, then the nozzle is installed and the pipeline is connected. The nozzle operation plan is prepared according to the oil quality and residue in the tank, and the nozzle is operated accordingly. During operation, it is necessary to adjust the operation plan at any time according to the inspection scale to meet the process requirements. Although the two kinds of storage tanks are basically the same in terms of cleaning process, there are obvious differences in cleaning process due to different nozzle installation positions.
1 Nozzle installation position
1.1 Tank top
1.1.1 Regardless of the volume of the arch tank, the middle part of the tank top is equipped with a safety valve and a breathing valve, which are basically arranged symmetrically in the center plate of the tank top. Under normal circumstances, the arch tank with a volume of less than 3000m3 needs to be equipped with a safety valve and a breathing valve. A 5,000m3 or 10,000m3 arch tank requires one safety valve and two breathing valves. A 20,00m3 or 3,00m3 arch tank requires two safety valves and two breathing valves (Figure 1a to Figure 1c). According to the design specifications, the breathing valve and safety valve on the top of the tank are determined according to the volume of the tank. What needs to be considered when cleaning is whether the opening hole on the top of the tank can be inserted into the nozzle (76mm). If the nozzle can be inserted into the opening hole on the top of the tank, the existing hole can be considered to install the nozzle. In fact, the diameter of the mounting hole of the breathing valve and the relief valve of the tank with a volume of more than 1000m3 is greater than 100mm, and the nozzle is smoothly installed without any problem. Before installing the nozzle, remove the breathing valve and safety valve, and then preform the nozzle fixing support according to the specifications of the flange. The diameter of the branch pipe is 108mm and the length is 200mm. The specifications of the flange are determined according to the connection port of the breathing valve or safety valve. The flange of fixing the support is connected with the pipe mouth of the tank top, and the nozzle is fixed on the nozzle support.
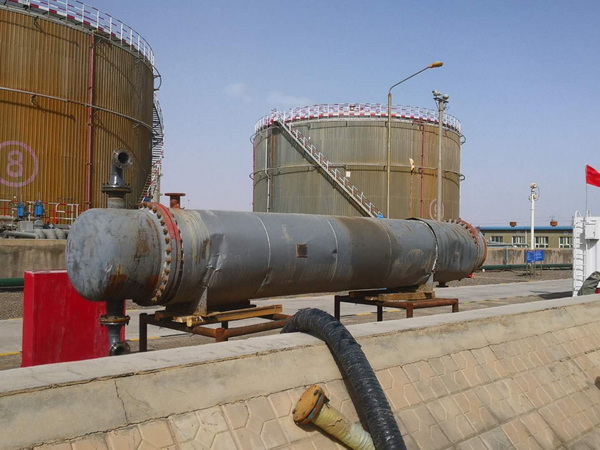
1.1.2 If the volume of the tank is not less than 10000m3, the diameter of the tank is usually more than 30m. If the nozzle is installed only using the nozzle of the existing breathing valve and safety valve on the top of the tank, the cleaning radius of the nozzle is about 15m, which seriously affects the cleaning effect. Even if the cleaning operation is carried out, the cleaning cycle and cost will increase. At this time, it is generally necessary to increase the temporary opening installation nozzle and increase the layout density of the nozzle. Temporary openings are usually arranged symmetrically, and are set to an even number and the total number is not less than 4 (a group of 2 when the nozzle is running), installed in the tank radius 1/3 (near the tank wall), one of the reasons is that the center of the tank bottom is higher than the surrounding, the sludge in the tank during the cleaning process is easy to move around, and the cleaning workload is relatively large; The second reason is that the center of the tank has been installed on the nozzle of the breathing valve and the safety valve, and the effective cleaning radius of the inner and outer ring nozzles can be effectively connected. Therefore, the position of the nozzle should be close to the tank wall and relatively dense, and the nozzle spacing is generally not more than 15m (Figure 4). Because the tank is full of a large number of toxic and harmful, flammable and explosive gases, in order to ensure safety, the opening of the tank top must be closed without fire opening operation, before opening the hole should be prepared: ① select the opening position, determine the number of opening holes, prepare the construction plan, and report to the owner for approval; ② Ensure operation standards and apply for operation tickets; ③ According to the curvature of the melon rind top plate of the selected opening position, prefabricated opening short nozzle; ④ According to Figure 2, the prefabricated nozzle fixing support, and the flange specifications are determined according to the perforated short nozzle flange (Figure 5, in which the curved plate, that is, the reinforcing plate, has an outer diameter of 310mm and an inner diameter of 98mm, its curvature is consistent with the top plate of the opening position, and its thickness is the same as that of the top plate). Tank top hole short nozzle size is not less than GB50341-2003 "Vertical cylindrical steel welded oil tank design code" requirements; ⑤ Prepare closed hole cutter, hole cutter (DN100) and center drill; ⑥ Prepare nitrogen and connect the pipe of the hole cutter to achieve gas protection. After the preparation work is completed, clean the anticorrosive layer of the top plate of the tank at the selected position with grinding wheel, sandpaper and wire brush, sand the adhesive surface to the metal body, and coarser it appropriately to clean the bottom surface of the curved plate in Figure 5 [5]. Use a metal binder (such as Mette iron, etc. [6]) that meets the requirements to glue the short nozzle to the top plate of the tank, and install a manual hole opener after the inspection meets the requirements. After cleaning, seal the short nozzle with a blind plate and keep it permanently. Before installing the opening machine, a small amount of oil needs to be added to the short nozzle of the opening hole to reduce the opening resistance and prevent sparks caused by collisions during the installation or opening process. After installing the hole opener, connect the nitrogen pipe to the air inlet of the hole opener to prepare for inflation. Calculate the hole stroke, immediately open the nitrogen valve after the center drill is opened, and pass nitrogen into the hole cutter for gas protection. After the holes are opened, close the nitrogen valve, remove the nitrogen pipe, take out the curved plate along with the hole cutter, install the nozzle fixing support, and finally install the nozzle and secure it. Check the hole cutter and center drill for damage, if any damage should be replaced immediately, and follow the same procedure for the next hole operation.
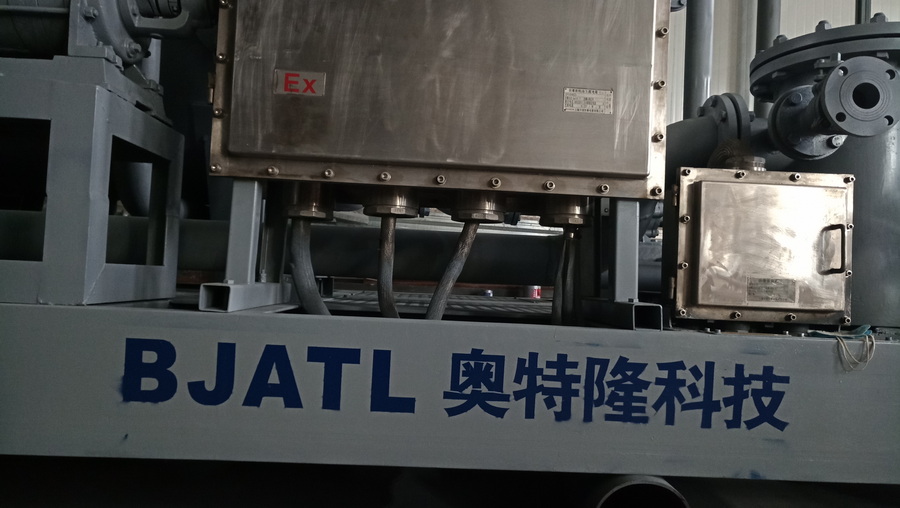
1.2 Tank wall manhole When the position or number of nozzles installed on the top of the tank cannot meet the requirements of cleaning operations, you can consider installing nozzles in the tank wall manhole, but make sure that the liquid level of the medium in the tank is below the manhole. Before installing the nozzle in the manhole, a temporary manhole cover for fixing the nozzle should be prefabricated (FIG. 7). The branch pipe size is 108×5. The outer diameter of the temporary manhole cover is the same as that of the manhole in the tank wall, and the thickness is not less than 20mm. After removing the manhole cover, clean the oil and rust on the surface of the manhole flange, replace the gasket, then install the temporary manhole cover, and finally fix the nozzle. After the nozzle is installed in place, manually rotate the nozzle for an all-round inspection to prevent internal debris from damaging the nozzle.
2 Vault tank mechanical cleaning operation
After the above preparation work is completed and the installation method of the vault tank cleaning machine is determined, the reasonable opening position of the tank top is first set according to the mechanical cleaning process of the oil storage tank, so as to determine the installation height of the cleaning machine, the cleaning radius, the number of the cleaning machine, the spray cleaning pressure of the nozzle and other cleaning process parameters to meet the needs of the cleaning operation. Secondly, make a strict cleaning operation plan according to the actual situation of the arch tank to be cleaned. Usually, the cleaning method of the cleaning machine is set as the bottom plate cleaning. First start the cleaning machine near the suction port (the opening hole of the arch top is set above the suction port) to ensure that the dissolved oil is concentrated near the suction port, then start the cleaning machine at other opening holes, and finally start the cleaning machine in the middle position. When the amount of sludge becomes less, the cleaning machine is adjusted to comprehensive cleaning, and the order of starting the cleaning machine is opposite to the above opening order. Due to the long range of the vaulted tank, in order to maintain the amount of cleaning liquid, it is necessary to pay attention to controlling the rotation speed of the nozzle to obtain the best cleaning effect.
3 Precautions
(1) Before opening the hole, the construction plan shall be submitted to the owner for approval, and relevant operation tickets shall be applied after approval, such as hot operation tickets, climbing operation tickets, electricity operation tickets, entry device operation tickets, etc. (2) When cleaning the anti-corrosion layer at the specified position of the tank top, manual methods must be used instead of mechanical methods to prevent sparks from causing unexpected catastrophic accidents. (3) Before installing the opening machine, a small amount of oil should be added in the opening short nozzle to increase and eliminate sparks. Before manually opening holes, make sure that the center drill is intact and slowly open holes to ensure that the cutting plate can be taken out by the center drill to prevent the cutting plate from falling into the tank and hitting the bottom plate and causing sparks or damage to the bottom plate. (4) Nitrogen injection should pay attention to two aspects: First, when manually opening holes, nitrogen should be injected after the center drill is opened to ensure that the working environment is in a safe state as shown in Figure 6 for cleaning the arch storage tank. Secondly, nitrogen (or inert gas) in the tank can dilute oxygen, and the volume fraction of oxygen should be ensured to be below the safety standard of 8% [7]. (5) Nitrogen is usually injected into the tank by breathing valve and safety valve orifice without nozzles on the tank top. If all orifice are installed with nozzles in accordance with the process requirements, nitrogen can be injected by means of oil measuring holes on the tank top, but the sealing of the joint must be ensured. (6) In the entire operation process, should be in accordance with the requirements of the standard operation, and use explosion-proof tools to prevent sparks.
|
|
|
|